Packaging Machine Repair Service: Making Certain Minimal Downtime and Maximum Efficiency
Packaging Machine Repair Service: Making Certain Minimal Downtime and Maximum Efficiency
Blog Article
Understanding the Secret Parts and Repair Work Strategies for Product Packaging Equipment Upkeep
Efficient maintenance of product packaging makers pivots on an extensive understanding of their vital elements, consisting of the framework, drive system, and sealing devices. Acknowledging typical maintenance issues, paired with the application of preventative techniques and troubleshooting methods, can significantly improve machine dependability. The choice of repair work methods, including the use of OEM components and the importance of certified specialists, plays an essential duty in decreasing downtime. To really understand the ins and outs of these systems and their upkeep, one should take into consideration the wider implications of disregarding these essential techniques.
Secret Components of Product Packaging Equipments
Packaging machines include several essential elements that interact to ensure efficient and effective product packaging procedures. At the core of these devices is the structure, which provides architectural stability and houses the various operating components. The drive system, commonly a mix of equipments and motors, helps with the movement of parts, allowing exact procedure throughout the packaging cycle.
An additional vital component is the conveyor system, which carries products with different phases of the packaging procedure. This is frequently enhanced by sensing units and controls that monitor the placement and rate of items, making certain synchronization and lessening errors. The filling up system is important for properly giving the appropriate amount of product right into packages, whether in fluid, powder, or solid type.
Sealing systems, including warmth sealers or adhesive applicators, play an essential function in safeguarding plans, stopping contamination and prolonging rack life. Additionally, identifying systems are important for providing necessary product details, making sure conformity with laws. The control panel, outfitted with easy to use user interfaces, enables drivers to handle maker functions, display efficiency, and make adjustments as required, making sure optimum productivity and performance in product packaging procedures.
Common Upkeep Concerns
Effective procedure of packaging equipments counts greatly on routine maintenance to protect against usual problems that can disrupt manufacturing. Among these problems, mechanical deterioration is prevalent, especially in components like conveyors, seals, and electric motors, which can lead to unforeseen downtimes. In addition, imbalance of parts can cause ineffective operation, causing items to be incorrectly packaged or harmed throughout the procedure.
One more common upkeep concern involves the buildup of dirt and debris, which can conflict with the equipment's sensors and moving parts. packaging machine repair service. This not just influences efficiency yet can additionally posture safety and security dangers. Lubrication failures can lead to enhanced rubbing, resulting in overheating and ultimate component failing.
Electrical issues, often coming from loosened connections or damaged circuitry, can disrupt machinery functions, leading to substantial production delays. Last but not least, software program problems due to obsolete programs or incorrect setups can hinder the machine's operation, requiring immediate treatment. Dealing with these typical maintenance problems proactively is necessary for guaranteeing optimum performance and long life of packaging equipment.
Preventative Upkeep Techniques
Carrying out preventative upkeep approaches is important for maintaining the effectiveness and integrity of product packaging machines. These methods encompass an organized strategy to upkeep, concentrating on published here the normal assessment and servicing of equipment to preempt potential failures. By adhering to a scheduled maintenance program, operators can identify deterioration on components before they result in substantial break downs.
Secret elements of a preventative maintenance technique include routine assessments, lubrication, component, and cleansing replacements based upon maker referrals. Using checklists can simplify this process, guaranteeing that no vital tasks are overlooked. Additionally, preserving precise records of maintenance activities help in tracking the maker's efficiency gradually, promoting notified decision-making relating to future maintenance requirements.
Educating personnel on the value of preventative upkeep boosts compliance and cultivates a culture of aggressive treatment. Executing a predictive maintenance part, utilizing data analytics and sensor technology, can additionally maximize equipment efficiency by forecasting failures prior to they happen.
Repairing Techniques
When encountered with breakdowns or ineffectiveness in packaging makers, using organized troubleshooting strategies is essential for identifying and settling issues quickly. The primary step in reliable troubleshooting is to establish a clear understanding of the equipment's functional specifications and performance metrics. This includes assessing the device's specs, along with any type of error codes or notifies displayed.
Next, operators must conduct a visual examination, checking for obvious indicators of damage, misalignment, or wear. This usually consists of checking out equipments, sensors, and belts to pinpoint prospective sources of malfunction. Collecting functional information, such as production rates and downtime logs, can additionally give insights into persisting problems.
As soon as potential problems are identified, using a logical technique to separate the origin is important. This might require screening private parts or systems in a controlled fashion. Involving in conversations with operators that connect with the machinery routinely can yield useful comments regarding unusual actions or patterns.

Repair and Substitute Best Practices
A thorough understanding of repair and replacement best techniques is crucial for preserving the longevity and performance of product packaging devices. Consistently analyzing the problem of equipment elements permits prompt intervention, preventing more substantial problems that can result in costly downtimes.
When repair services are essential, it is crucial to utilize OEM (Original Tools Supplier) components to guarantee compatibility and performance. This not only protects the integrity of the machine yet also maintains warranty agreements. Furthermore, it is advisable to preserve a stock of vital spare parts to promote quick substitutes and decrease functional disruptions.
For complicated repair work, involving qualified professionals with specialized training in packaging machinery is recommended. They have the knowledge to diagnose concerns accurately and execute repair work successfully. Recording all fixing activities and parts replacements is essential for keeping a detailed upkeep history, go right here which can assist in future troubleshooting.
Finally, applying an aggressive approach, consisting of routine evaluations and anticipating maintenance strategies, improves the reliability of product packaging machines. By sticking to these finest methods, organizations can ensure optimal equipment efficiency, decrease functional threats, and prolong equipment life-span.
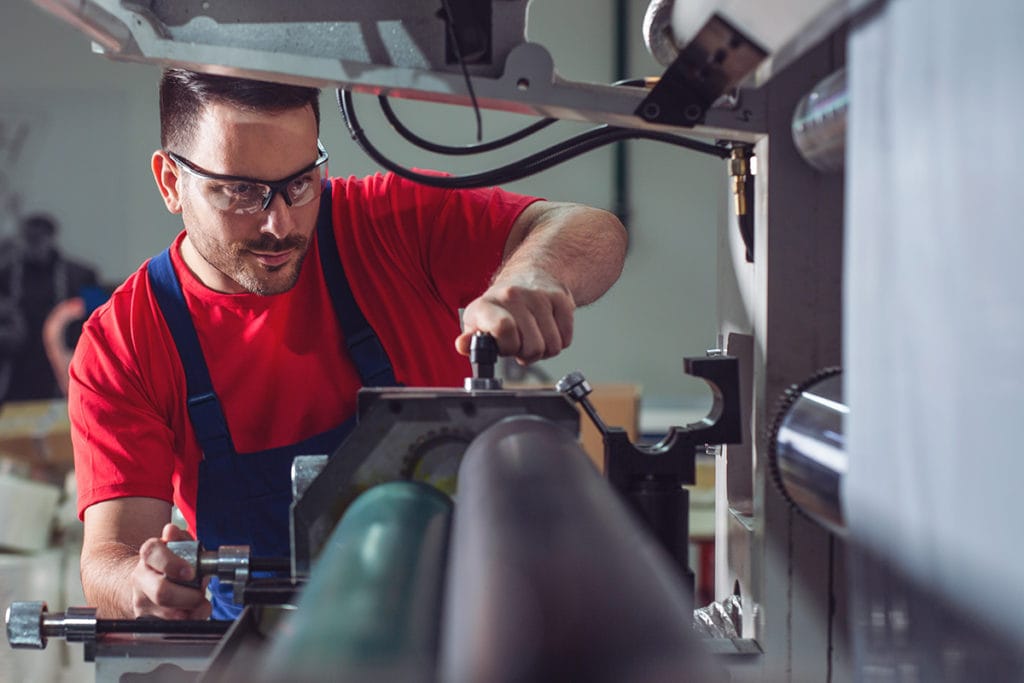
Final Thought
Finally, a detailed understanding of packaging maker parts and effective maintenance methods is vital for ideal performance. Normal evaluations and making use of OEM components can significantly reduce downtime, while a well-documented upkeep history cultivates proactive treatment. Employing certified professionals better improves repair Click Here service top quality and dependability. By implementing these practices, companies can guarantee the durability and efficiency of packaging makers, inevitably adding to improved functional productivity and minimized costs.
Reliable maintenance of product packaging makers hinges on an extensive understanding of their vital components, including the framework, drive system, and sealing systems.Reliable procedure of packaging equipments relies greatly on regular maintenance to prevent common concerns that can interfere with production.Carrying out preventative upkeep approaches is vital for maintaining the efficiency and reliability of packaging makers. Furthermore, maintaining exact records of maintenance tasks help in tracking the equipment's efficiency over time, assisting in educated decision-making regarding future upkeep needs.
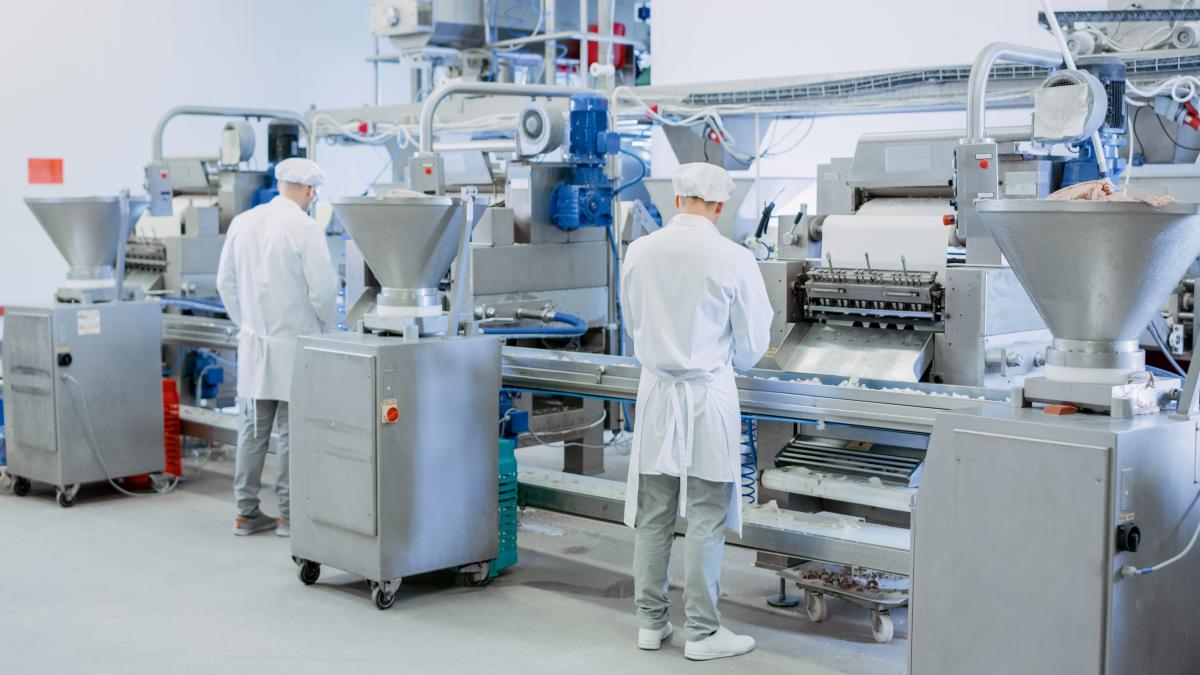
Report this page